Technology to cut down on defects
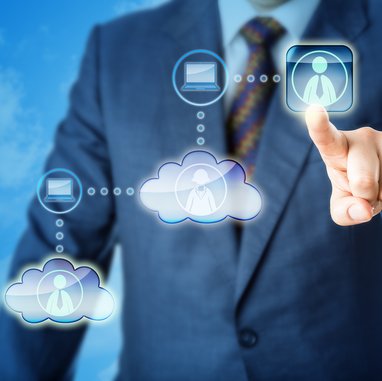
As digitalization becomes the new buzzword in the fashion world, new challenges appear for shoe manufacturers. To ensure businesses are ready to turn them into opportunities, the concepts developed by the Industry 4.0. have to become familiar to all decision makers
After bringing you some flavour about additive manufacturing (READ FULL ARTICLE HERE) and the concepts of automation and advanced robotic (READ FULL ARTICLE HERE), today we present you some technology applications to cut down on defects.
The implementation of management quality standards or lean practices, and other methods that reduce waste and defects, have allowed companies to improve their performance in terms of efficiency, but it is still very manual in several cases. Relying on humans to record workmanship on paper, data collection turns into a chore. The data can be collected every hour for ten years, but that doesn’t mean the company get the most out of it. If a deviation happens in one work unit, and its team resolves the problem in offline mode, it is hard to perform a gap analysis. Besides, the problem can get worse because a team that solves a problem on its own doesn’t have data on the root causes. Thus, companies face some difficulties to tackle problems on a consistent basis, and problems will continue to pop-up and dissipate.
Some of the latest trends in manufacturing technology can be found in a study named ‘Exponential Technologies in Manufacturing’, carried out by Deloitte in collaboration with the Council on Competitiveness and Singularity University (SU). Some of the main highlights include:
• Among the exponential technologies that can enable transformational growth in manufacturing, the top technology investment areas for manufacturers include, advanced analytics, modelling and simulation, and Internet of Things (IoT) platforms
• Innovation enabled by exponential technologies can help manufacturers grow faster, be more agile, and unlock new forms of value
• Talent continues to be a key competitive differentiator
• Business and government research activities, along with venture capital investments contribute to innovation ecosystems
• Among the exponential technologies that can enable transformational growth in manufacturing, the top technology investment areas for manufacturers include, advanced analytics, modelling and simulation, and Internet of Things (IoT) platforms
• Innovation enabled by exponential technologies can help manufacturers grow faster, be more agile, and unlock new forms of value
• Talent continues to be a key competitive differentiator
• Business and government research activities, along with venture capital investments contribute to innovation ecosystems
To bring some of the insights of this study into the traditionally labour-intensive footwear industry, might be interesting as digitalization of fashion is slowly becoming a widespread practice. Shoe manufacturing companies are partnering with software development companies for digitizing their shop floors and replace paper forms with its manufacturing apps - tailored to the companies’ exact requirements - that run on tablets or other touchscreen devices. Workers don’t need information technology expertise to use the system. For instance, in the case of defects, they call up an image of the shoe style they are working on and note where the defects are. The apps are connected to the production equipment allowing to correlate machine and human data using the built-in analytics engine. By giving the material suppliers clear and accurate data from the production lines, companies can remove ambiguity and delays when solving problems. With this sort of digital solutions, companies are able to capture all their production data in real-time, get visibility into the root causes of production issues and can feed it all the way back to the designer. More broadly, the data can also be used to track production factory to factory and value stream to value stream.
Generally, companies are bringing on individual pieces of technology and equipment that can be quickly deployed in their factories, because they need to maintain flexibility and adaptability to customer demands this transformation is happening step by step.
By looking at how to connect individual solutions using a digital backbone for a more comprehensive approach, companies are moving toward taking digital from design all the way to the factory floor. This turns out to be a very ambitious picture and may be difficult for a wide range of products. However, to generate hybrid solutions that allow the system to be flexible between analogue and digital approaches as needed, it might be the most likely future result.